Logistics is the bridge that connects the manufacturer to consumer . The share of warehousing is only 14–34% of total logistics cost but it is the backbone of supply chain network during various stages of transportation.
Warehouse standards in Unorganized warehousing sectorThe share of organised indian warehousing industry is growing and developing Grade A warehouses however the industry is still dominated by unorganized fragmented players.
The warehousing demand is being tapped as an investment opportunity and many people are investing in building warehouses in unorganized market especially in Tier 2–3 same cities.
However due to lack of logistics expertise majority of new investors end up building warehouses which do not meet the warehousing standards and becomes liability rather than investment. These sub standard warehouses may get leased in first few years due to demand and supply factor but in some years they become redundant with new better infrastructure in their vicinity.
It cannot be denied that majority of unorganized players will not be able to meet grade A warehouse standards due to lack of funds however if below mentioned basic parameters are taken care of during building warehouse the chances of its getting frequently leased and at better value is very high and the return of investment will be high for long term.
General Parameters- Locality : Location is a crucial element in deciding the value of warehouse. The locality should be safe, secure and strategic depending on logistics requirement of that city.
- The location of warehouse should be on highway or have easy access to same if logistics in your city mainly serves as a transit hub or link for supply to other cities. The transport will avoid unnecessary transit to cities & save time.
- The location of warehouse should be areas which can cater entire city if warehouses are required for internal distribution in city by the companies.
- If the purpose of warehouse is for manufacturing hub/city select the the industrial area or permitted zones where client can easily get pollution certificates & other licenses.
- Commercial Land : The warehouse should be build on commercial land and not on agricultural or residential plots. The municipality records, property tax receipts and electricity bills should be in order. The economy becoming more formal and companies adhering to government regulations it significantly increases the chances of your warehouses to be leased and on better valuation then other warehouses in your area.
- Labour Availability: Indian warehousing operations are still labor intensive. They employ minimum labor workforce on full time basis and mainly dependent on demand labour due to operational dynamics. Always ensure that warehouse is build in area where there is easy availability of labour.
- Connectivity: The warehouse location having proper connectivity to city, public transport, hospitals, railway station, airport plays an important role when client chose to lease a warehouse. The daily workforce in warehouses (Supervisors, managers, pickers etc) should be able to easily commute to warehouse from residential areas. The location should be serviceable for all courier companies as courier is an important part of logistics operations mainly for e-commerce businesses.
- Parking: The majority investor concentrate on build up area and consider open area as waste of opportunity. It is vital that 10–15% of area is allocated for parking or vehicle movement as warehousing and transport are interlinked.
- Vehicle Access : The logistics involves frequent movement of vehicle like Tata 407, Eicher, 20/40 Ft. containers to and from warehouse. The warehouse should have easy access of 20/40 Ft container vehicles to warehouse and space for angular movements. It could be the DECIDING factor for clients to lease the warehouse.
- Toilets: At least one toilet for smaller warehouses and separate toilets for staffs and labors in big warehouses.
- Rest room for labours, guard rooms, office rooms, communication rooms for bigger warehouses
- Power Back Up
In both the cases it is important to consider that locality has proper entry and exit points and is not congested by city traffic because it can be big negative for your warehouse.
Few other important parameters which can act as catalyst for increasing chances of your warehouse to be leased
- Warehouse height: The optimization of warehouse space is prime factor in profitability of warehousing operations. The warehouse height plays an important role in space optimization either by installing racking system or stacking products to the possible level. For mid size warehouses the recommended height is minimum 30 ft and for bigger warehouses minimum height to be 35–40 Ft.
- Flooring & Racking: The base of warehouse is floor and its strength determines the value of warehouse. The strength of the flooring is important aspect to install heavy duty racks or machines. It may not be important deterrent in smaller warehouses as they don’t undergo racking but should be sufficient to withstand installation of basic machines for manufacturing. But bigger warehouses should go for Vacuum Dewatered Flooring (VDF) & 8 Metric Tonnage Load Balancing for 1 sq.mt. floor Area.
- Docks: Docks are used for loading/unloading of goods between vehicle & warehouse. 60% of warehouse in india are leased by logistics company and they have frequent movement of products to and from warehouse. The warehouse becomes unusable for logistics and they will not lease it if warehouse do not have adequate no of docks . Based on analysis of leads received by us for leasing it is recommended to have minimum 2 docks per 5000 Sq.Ft. area of warehouse.
- Warehouse Layout: The warehouse layout and design is extensive subject and we will guide on this in a separate blog. We recommend to always consult warehouse consultant with extensive experience. The warehouse design layout should consider usage of every inch of space, proper flow, minimum pillars/obstructions, minimum time to move from one end to other.
- Few other important technical aspects which are important deterrent for bigger warehouses
- Skylight : Mostly for bigger warehouses. 3% of total roof area.
- Proper Ventilation for all size of warehouses.
- Roof Insulation for bigger warehouses.
- Dock levelers and canopy for bigger warehouses.
The below table is our recommendation for and ideal serviceable warehouse.
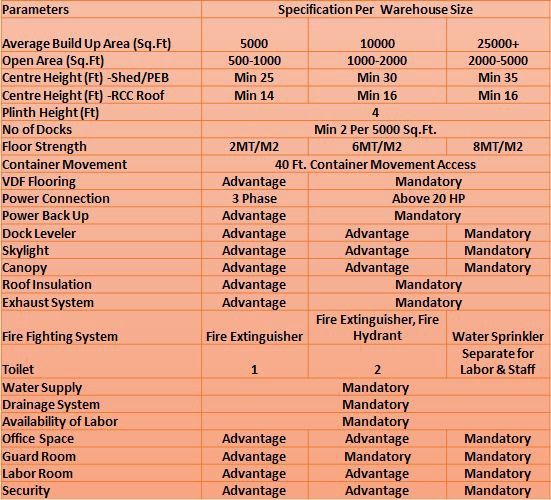
*Advantage : Not mandatory but if present these specification can be advantage for the warehouse and increase its value compared to warehouse in neighborhood
Regards,
Godamwale Team